The plastic molding process starts with designing the desired product. Then, a mold or tool is created to shape and create multiple copies of the product.
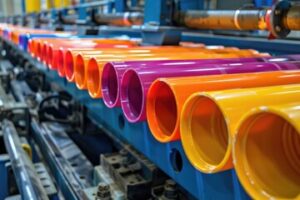
Proper structure design helps lengthen the lifespan of injection molds. Slower cycle times, appropriate clamp force and temperature control also help with longevity. Read on American Plastic Molds for further info.
The rotational molding process is a popular method for creating hollow products such as tanks, containers, and pipes. It uses a powdered polymer (most commonly, polyethylene) that is placed inside of a metal mold and then slowly rotated while being heated. This allows the plastic to melt onto the walls of the mold and take on its desired shape. The rotational molding process is capable of producing larger and double-walled parts, but it has a number of disadvantages including high cycle times due to long heating and cooling cycles, limited material options, and the difficulty in incorporating certain design features such as text, writing, or symbols.
The molds used in rotational molding are typically made from aluminum or steel. This is because they must be able to withstand the high temperatures during the heating and rotational processes. The metal is also used to provide a stable base for the finished product. The molds are usually designed with a draft angle to make it easier for operators to remove the finished part from the mould once the heating, cooling, and rotational processes have been completed.
Once the plastic is molded, it must be removed from the mould and cooled. The cooling process is critical because too fast a temperature change can cause the plastic to deform or warp. A slow and steady cooling rate is preferable because it allows the polymer to cool evenly.
When the plastic is being ejected from the mould, it must be drawn away from the runner and sprue systems by components called tunnel gates. These are located on the side of the mold that opens first when the mould is cooled and rotated. The sprue and runner systems are then cut off by the machine during the cutting process.
The ejection system is important because it ensures the safe and damage-free removal of the molded plastic from the mould. This system consists of guiding and positioning components that include a sliding ejector pin, slide angle pins, sliders, and locking blocks. In addition, for molded plastic parts with lateral projections or holes, a system of components called lifters can be used to pull them away from the runner and sprue system when the mould opens.
Injection Moulding
Injection moulding is one of the most widely used production methods for making plastic parts. It is a highly efficient process that provides high precision and repeatability, along with low unit cost. It is ideal for producing large quantities of plastic products with tight dimensional tolerances, such as wire spools, plastic packaging, bottle tops, toys, combs, and chairs. It is also a great choice for producing parts that require complex designs and stringent specifications.
The injection moulding process involves the use of a plastic polymer, or resin. The molten plastic is injected into the molds under controlled pressure. The injected plastic then cools, hardens, and solidifies to form the desired shape. This method is very versatile and accommodates a wide variety of polymers, including both thermoplastics and thermosetting plastics.
To ensure that the injected plastic is evenly distributed, manufacturers use a tool called a plunger or screw to push it into the mold cavities. The amount of force required to inject the plastic is determined by the viscosity of the polymer and its shear rate. The injection speed is adjusted accordingly. The temperature of the injected plastic is also regulated to prevent overheating.
Once the molded plastic has cooled, it is removed from the molds. The molded product must be completely free from defects such as warping, sink holes, bubbles, and uneven wall thicknesses. To avoid these problems, the plastic must be cooled uniformly and the mold must have good drainage and venting.
Injection molding is a highly automated process, reducing the need for manual labor and improving quality control. However, it is not the best option for small plastic parts that need to be molded in a limited time frame, as it can cause the material to lose its elasticity.
Another disadvantage of injection molding is that it can be expensive to produce complex shapes and parts with narrow dimensional tolerances. This is because the injection machine requires expensive metal parts, such as a die and core, that are typically made through standard machining or Electrical Discharge Machining (EDM). To reduce these costs, some plastic manufacturers use aluminium moulds.
Pressure Moulding
This molding method uses a high amount of heat and pressure to transform polymers into the desired shapes. The material is placed inside a hollow mold that’s then closed and subjected to varying amounts of heat and pressure until it takes the shape of the mold. This process is often used for manufacturing larger plastic products like car bumpers. This type of molding is also commonly known as compression moulding.
While this process is useful for manufacturing large parts, it can be expensive to use and requires more time to complete than other methods of molding. Additionally, this type of molding is best suited for thicker parts such as car body panels.
The primary benefits of this process are its ability to produce a high number of identical parts and its ability to handle a wide range of materials. It can be used to manufacture both plastic and metal parts, making it a versatile option for manufacturers that need to produce a wide variety of products.
This defect occurs when the molten plastic fails to completely fill sharp internal corners or edges within the mold cavity. This can be caused by improper handling, moisture in the raw material, or inadequate injection pressure. To avoid this, optimize the injection pressure, melt and mold temperature, and venting channels to direct uniform melt flow.
Another common problem is excessive flashing, which occurs when the molded plastic extends beyond the mold’s boundary walls. This can be caused by inadequate injection pressure, excessive heat, or incorrect cooling conditions. To prevent this, optimize the injection pressure, adjust the heat and cooling conditions, and make sure that the gate is properly closed.
Another potential issue is excessive shrinkage, which can be caused by insufficient injection pressure, uneven cooling, or rapid mold shutdown. To avoid this, optimize the injection pressure and mold temperature, increase the melt flow rate if necessary, and use the proper molding conditions. In addition, ensure that the gate is properly closed and that ejector pins retract correctly. It’s also important to remember that it’s the holding pressure that determines shrinkage, not the initial injection pressure.
Sheet Moulding
Sheet molding compound (SMC) is a ready to mould glass fibre reinforced polyester material primarily used in compression moulding. It’s manufactured in a continuous in-line process by dispersing long strands of chopped fiber (typically carbon or glass) on a bath of thermoset resin, usually polyester, vinyl ester, or epoxy resin. The longer fibers give SMC a higher strength than standard bulk moulding compounds (BMC).
The resin and fillers in SMC are mixed to form a paste, which is then sheathed both top and bottom with a film to prevent auto-adhesion and placed inside the press where it’s heated and compressed. Up to 2000 psi is applied which gives the SMC enough pressure to spread and fill every part of the mold, producing a highly detailed and accurate product.
SMC is a good alternative to metal for products that require high load-bearing capabilities. It also has excellent corrosion resistance, particularly to salts and chemicals. This means SMC parts can often be used in harsh environments, such as marine applications or automotive components. This is because SMC can withstand high levels of impact and stress that would otherwise be damaging to metals.
Like other forms of composite, SMC is relatively lightweight. This allows for the production of components with a low weight and cost. This makes it an ideal material for things like bathtubs and hydrotherapy pools, as well as seating in arenas, cinemas, and stadiums. It can also be molded into complex shapes to accommodate different needs, making it an ideal alternative to traditional fiberglass.
The SMC production process is fairly quick. Once the charge has been poured into the mould, it’s heated and compressed in as little as a minute per piece. This is a big draw for producers, as it means they can produce large numbers of finished products quickly and accurately.
SMC is a very versatile plastic, able to be molded into complex designs with precise dimensions. It can even be primed in-mould to achieve a class A finish, which saves time and money on the paint finishing process. For these reasons, it’s the most popular choice for automotive exteriors and interior components.